Maintenance Welding Vs. Fabrication Welding: The Right Alloy for The Right Job
By Pat A.
When you think of welding do you picture sparks flying in the air as shiny new tractors roll along assembly lines in clean, temperature-controlled factories? Most people do, and it’s no wonder, as over 80% of the welding products used every day in North America are used in the manufacturing of products, from tractors to lawn chairs and everything else in between.
Generally speaking, this type of welding is called fabrication welding, but there is another kind of welding… Maintenance welding.
Once that tractor rolls off the assembly line, things change quickly. That new tractor is now in the field working hard. It becomes old, wet and dirty, and after enough time and stress it breaks. This is when you need maintenance welding and is exactly the type of situation that Rockmount products are made for.
This is when you need maintenance welding and is exactly the type of situation that Rockmount products are made for.
You could technically use fabrication welding materials, such as 7018 or ER70 S-6, in a maintenance environment, but the truth is they just weren’t made for this kind of job. Here’s why.
Fabrication welds are typically done:
- On clean metal
- On flat applications
- On identifiable metals
- By a welder with experience repeating the same weld
Standard welding materials are specifically made to fit these conditions and produce the most economical weld possible.
In comparison, maintenance welders work in much tougher conditions. Maintenance welding is commonly done:
- On contaminated metals: Weld, rust, dirt, and oil all build up over time and the welder often can’t clean the base metal the way they would prefer.
- Out of position: Maintenance welds are often made in hard to reach places.
- On unidentifiable or dissimilar metals: Base metals can vary widely although they look the same.
- Exact base metal identification can be very tough for a maintenance welder. Sometimes just getting close is all that they can do.
- With less experience: While most maintenance welders are highly skilled, they commonly weld on something they have never seen before, in situations they have never been in before.
The work that maintenance welders do in the field is very different to the work a fabricator does in a factory, and for that reason it’s unrealistic to expect that same tool can be used for both jobs.
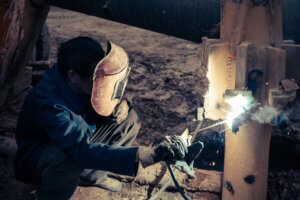
Rockmount’s maintenance welding products are specifically designed for the tough conditions in which maintenance welders operate.
Rockmount’s maintenance welding products are specifically designed for the tough conditions in which maintenance welders operate. Just to give a few examples:
- Brutus is designed to weld any steel including stainless, and is ideal for repairing unidentifiable or dissimilar metals. Brutus can also be used to extract broken bolts.
- Tartan products will easily weld out of position through oil, rust and dirt and work great on galvanized. They also strike incredibly well making them ideal for all levels of welder.
- Polaris products produce both strong and ductile welds on contaminated steels making it ideal for repairing cracks in heavy equipment.
As told to us by the owner of a large construction company:
“One day I asked my welder why he was using that more expensive Rockmount welding rod. He told me that Polaris A is the reason we went from repairing excavator buckets once a month to doing them once a year. I just walked away and never questioned it again. Rockmount literally saves us tens of thousands of dollars on repairs each year.”
“Rockmount literally saves us tens of thousands of dollars on repairs each year.”
Rockmount products are designed to Weld Stronger and Last Longer, and when it comes to maintenance welding, they are the right tool for the job.